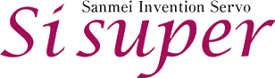
Si super is the ultimate stepping servo motor system equipped with the 12bit encoder and our own positioning algorithm.
Model | Si-02DS | ||||
---|---|---|---|---|---|
Application motor * (B) is with brake |
SM-L5M SM-02MH(B) SM-04MH(B) SM-09MH(B) SM-12MH(B) |
||||
Rated output current (A0-p) | 2 | ||||
Maximum output current (A0-p) | 4 | ||||
Control mode |
Servo control mode / step control mode Switch by parameter |
||||
Control method | Transistor PWM (sine wave drive) | ||||
Allowable load inertia | 30 times of motor inertia | ||||
Position feedback | 12-bit one revolution absolute encoder (4096 resolution) | ||||
Outline dimensions (mm) | W34, H98, D80 | ||||
Outline Mass (kg) | 0.24 | ||||
![]() |
Feed voltage
(V) |
Motive power | DC24V±10% | ||
Control power | DC24V±10% | ||||
Supply current (A) |
Power current (A) | 2.0 (MAX4.0) | |||
Control current (A) | 0.4 | ||||
Position command system | Position command pulse train | ||||
![]() |
Operating temperature | 0 to +50 ℃ | |||
Storage temperature | -20 to +85 ℃ | ||||
Operation and storage humidity | Less than 90% RH (non-condensing) | ||||
Seismic motion | 0.5G | ||||
Shock resistance | 2G | ||||
![]() |
Regeneration capability | Built-in, The regenerative processing circuit can be connected to the outside (option). | |||
Electronic gear |
The motor revolution by setting the electronic gear (32,768 × 1/65,535) to (32,768 × 65,535/1) can be driven with a pulse The two-stage switchable by the control input |
||||
Overtravel prevention function |
Hardware OT, software OT (Select the Enable / Disable by the parameter) |
||||
Point table positioning | No | ||||
Homing | 1 rotation absolute initial position pulse train output, built-in homing function | ||||
Jog | There is a simple function for commissioning. | ||||
Step feed operation | There is a simple function for commissioning. | ||||
Speed control operation | No | ||||
Torque limiting function |
Normal time forward / reverse torque limit (set in parameter) The forward rotation of the control input / 5 stage switching for reverse torque limit (Each torque limit value is set by parameter) |
||||
Monitoring facility |
LED 1 point (alarm display by blinking) Numerical monitor by USB connection (dedicated PC monitor software screen display) |
||||
Protective function |
Body EEPROM error, motor EEPROM error, encoder error, System malfunction, excessive position deviation, A-phase overcurrent, B-phase overcurrent, Operating temperature abnormality, overload, power supply overvoltage, power supply voltage down, control power failure |
||||
Multi-axis connection function | (Multiple axes can be set and adjusted by connecting using a USB hub) | ||||
Serial communication I / F |
USB 1ch (Full-Speed Function) (Parameter setting, for the dedicated PC monitor software) |
||||
Standards, environmental compatibility | UL compliance / CE (self-declared) / RoHS correspondence |
Option name | Models | m number |
---|---|---|
Motor cable | SiS-MCB□□M | 3,5,10 |
Encoder cable | SiS-ECB□□M | 3,5,10 |
Supply cable | SiS-PWBC03M | 3 |
I / O cable | SiS-IOB03M | 3 |
I / O cable | SiS-IOPLS03M | 3 |
Regenerative cable | Si-RGVC | 1 |
Pulse output cable | SiS-PLS03M | 3 |